Pin and female connectors are widely used and are commonly found on circuit boards. Quality is a fundamental factor affecting electrical performance and process flow. Common quality problems include pinhole defects, unqualified flatness, insufficient retention rate, and rubber materials that do not meet temperature resistance standards. Then, Konnra connector manufacturer will come and learn about the quality of pin and female connectors and how to ensure the stability of the product.
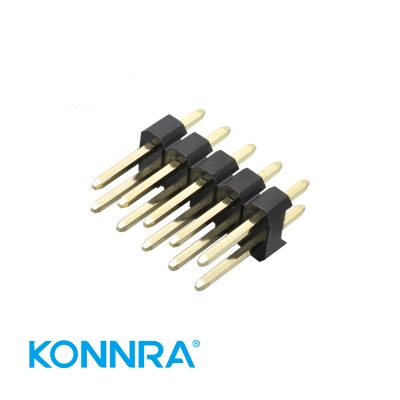
- During the production process, missing pin headers and pin headers need to go through the assembly process, and stitches will appear. How to ensure that inferior products do not flow into the hands of customers is one of the key factors affecting the production quality of an enterprise. Although each product has been thoroughly inspected, visual fatigue is unavoidable for workers during visual inspection. Ordinary manufacturers have added active detection equipment for missing needles on their machines to ensure that products with missing needles will be screened out. Machine and human control are the main ways to increase production.
- For end soldering of circuit boards with unqualified flatness,SMTpasting is one of the essential processes. Pin rowing, wrapping mother rolls, and automatic pasting can improve production efficiency and reduce labor costs. So when choosing SMT products, what you worry about is flatness. Once a defect occurs, the product will be unable to conduct electricity due to weak soldering. The re-soldering process is lengthy and adds cost.
How to ensure product stability?
- Screening of machine fixtures. Control the fixture to adjust the flatness to 8-10S. When the product smoothly passes through the clamp and enters the pipe, the flatness is qualified. When the product is pasted, the flatness does not meet the requirements. Place it in the defective area and check again after checking.
- Secondary inspection of the instrument. For products that cannot complete active machine inspection and cannot pass the fixture, use CCD to check flatness analysis. After checking the flatness, proactively enter the carrier tape packaging process.
- Insufficient strength
Retention force is an issue that cannot be ignored in the performance test of pin headers and header headers, but it often causes serious quality accidents. For example, the fastening force between the busbar rubber core and the terminal is insufficient, which is difficult to detect when welding the PCB. Once the butt welding with the bus bar is completed, if the welding is completed and the bus bar is inserted, the bus bar rubber core will all be taken out, leaving only the bus bar terminals on the PCB. This batch of bad behavior will bring serious economic losses to the enterprise.
How to control this link? After the terminals or rubber cores are produced, they must be matched first and tested to see if the holding force and insertion and extraction force are within a reasonable range. They can only be put into storage after passing the test. During product assembly, strict sample retention and plug-in testing are conducted on the three sampling steps of a patrol product, and detailed data records are made. The product must be tested layer by layer before leaving the factory.
- Currently, PBT, PA6T, PA9T, and LCP are commonly used as plastic raw materials for high-temperature pin headers. Among them, PBT is only suitable for wave soldering, while the three types of welding machines, PA6T, PA9T, and LCP, can be used for wave soldering and reflow soldering. Product patches must be reflow soldered, so when customers ask for samples, you must understand the customer’s processing technology. Even if high-temperature-resistant raw materials are used, problems such as deformation and foaming of the rubber core may occur when passing through the furnaceWhy?
One of the reasons is that if PA6T, PA9T, and LCP materials are not used for three to three months after production, moisture in the materials will cause foaming and deformation during welding. Therefore, when the plastic raw materials have been stored for 1 to 3 months and have not been used, they need to be baked again and reflow tested to confirm whether there is deformation or blistering. Normal shipment can only be made after passing the test.
The above explained content is about what is the key to the quality of pin header and header connectors and how to ensure the stability of the product. I hope it will be helpful to you after reading it. If you want to know more about header headers For connector related content, you can consult online customer service, and we will serve you wholeheartedly. Dongguan Konnra Electronics Co., Ltd. is a manufacturer specializing in connectors, connecting wires, electronic wiring harnesses and other connectors for more than 20 years. Its main products include connectors, pin headers and female headers, connectors, connecting wires, wiring harnesses, electronic wires, Wire-to-board connectors, wire-to-wire connectors, etc. The company has complete qualification certificates, strong technical force, sophisticated processing equipment, complete inspection equipment and strong R&D capabilities. It provides you with green, environmentally friendly and high-quality connectors and wire harnesses, and is your most loyal and reliable partner.