Today’s LED lighting industry applications can achieve higher efficiency and better performance through the use of high-density and small-size connectors. Support automated manufacturing, withstand harsh environmental conditions, facilitate installation, comply with specifications, and achieve design goals. The unique electrical and mechanical properties of the connectors are essential.
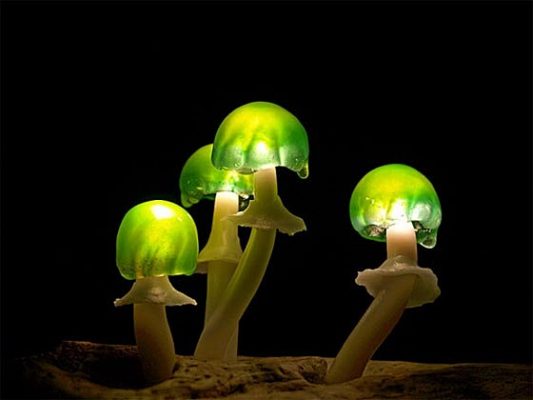
First, the electrical characteristics of LED lighting
Before delving into the size, fit and function of the connector, ensure that its electrical characteristics meet expectations. Including rated voltage, withstand voltage, rated current, current derating, contact resistance, insulation resistance and rated operating temperature.
Rated voltage: The rated voltage of the connector, or operating voltage, is the maximum continuous voltage during normal operation without physical deformation or electrical failure. The voltage rating of the connector is determined by its insulating material characteristics and contact spacing requirements.
Withstand voltage: Withstand voltage is the highest potential difference voltage that the connector can handle before reaching the breakdown voltage or interrupt voltage discharge. Connectors are tested near the breakdown voltage, and at their withstand voltage, usually around 75% of the breakdown voltage, should ensure safe use without arcing on the surface. Voltage resistance depends on the connector’s insulation, clearance distance, and creepage distance, and a higher voltage resistance indicates a lower likelihood of surface arc failure. However, the application environment and operating conditions may affect these results.
Rated current: The rated current or working current of the connector refers to the nominal maximum current in amps (A), which is determined by the contact material, the contact resistance of the conductive element with the surface and the operating temperature. The designer should select the rated current that meets the temperature and heat dissipation requirements of the application.
Second, the mechanical characteristics of LED lighting
Wire gauge: The wire gauge is usually expressed as the size range of wires to which the wire-to-board and wire-to-wire connectors fit, and they determine the maximum current carrying capacity of the wire. Design engineers must define the range of wire gauges that are safe for their applications and take into account sufficient derating requirements to ensure the compatibility of their connectors.
Plug and plug forces: These characteristics describe the forces required to fit and separate a pair of connectors and are directly affected by connector design characteristics, including locking characteristics, wire gauges, crimp design, and crimp quality. The insertion force of the connector directly affects its impact and vibration performance in harsh environments.
Durability: The durability of a connector is determined by the maximum fit cycle it can withstand before any component wears out to the point of failure. If the connector is operating within its rating and below its maximum number of durability cycles, its specified electrical characteristics should also be stated.
Design engineers selecting new connector solutions often struggle to identify which connector features are most optimized or improved. Manual welding has an inherent labor cost, but can result in reduced connector consistency, reduced quality, and less robust and unreliable connections. Low-cost, hand-welded connections are not suitable for high-reliability, harsh environment LED lighting applications. This industry often requires surface mount connector solutions that are easy to assemble without the need for complex or expensive tools.
In addition to ensuring that the electrical and mechanical characteristics of connectors meet application requirements, the evaluation connector must comply with relevant regulatory requirements, adequately demonstrate the cost of its components, perform reliably throughout the product life cycle, and support repeatable manufacturing, reducing manual labor, rework, testing, and additional costs associated with these processes.
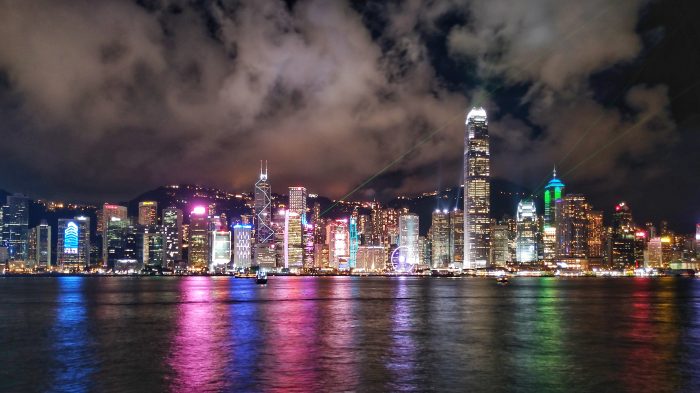
When choosing connectors for LED lighting industry applications, design engineers should consider the characteristics of the connectors identified, how to improve their design efficiency, performance, etc. While traditional connectors may cost better, today’s advanced connectivity solutions offer a range of features and benefits that fully demonstrate their advantages in meeting demanding electrical, mechanical, manufacturability, reliability, cost, and availability requirements.