Among the many performance indicators of connectors, stability and reliability are very important factors. A connector that is “very durable” usually means: it can withstand higher mechanical shock and vibration stress; it can still maintain mechanical and electrical integrity after being exposed to harsh environments or multiple plugging and unplugging; and it has excellent EMI Shielding performance.
To evaluate the durability of connectors, various industry standards have been developed.
Key contact point design
It can be known that there must be many ways to build a durable connector. Contact design, insulator shell, locking mechanism, EMI shielding, PCB assembly, etc. all require more comprehensive consideration and targeted optimization. Of course, According to the constraints of practical applications (such as cost, appearance, etc.), various functions and features are reasonably configured, and finally a solution that meets specific design needs is formed.
Among the many factors that affect connector durability, contact design is one of the most important elements and the most basic link. Almost all durable products will inevitably make a fuss in this aspect. After all, the contacts are the key to directly affecting the electrical characteristics of the connector.
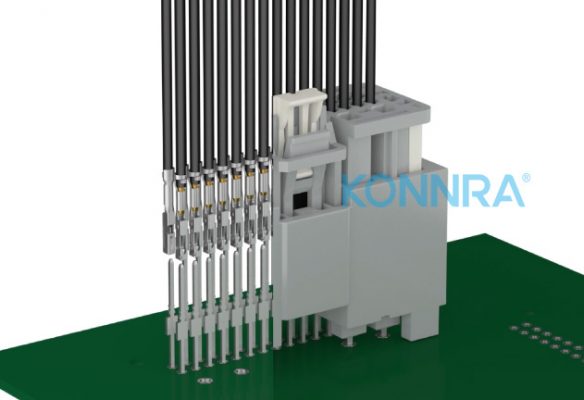
Observing the contact design of these fine-pitch board-to-board connectors, we will find the following aspects:
Contact material
Generally speaking, beryllium bronze (BeCu) is more popular for durable connectors than brass and phosphor bronze, two low-cost conductor materials. This is mainly because it has good mechanical elasticity. Once it is molded and hardened, it can maintain its shape in complex environments or repeated plugging and unplugging. This feature is important for providing higher mechanical strength and electrical performance and improving the reliability and durability of the connector. Sex is obviously more beneficial.
Mechanical structure
Most durable connectors have multi-finger, multi-faceted contact structures, or extend the sliding range and insertion depth of the contact insulator to increase the contact area as much as possible, so that the connector can obtain excellent electrical characteristics and ensure the stability and continuity of the connection.
Plating
Gold plating and tin plating are two important options for optimizing user connector durability. The former is the best choice for low-contact PCB long-life, high-reliability applications; the latter is low-cost, has good solderability, and is also suitable for high normal force contacts. Therefore, in practical applications, a contact design solution that has the best of both worlds is: gold plating in the key mating area related to reliability, and tin plating in the connector tail area to obtain better solderability and low cost advantages.
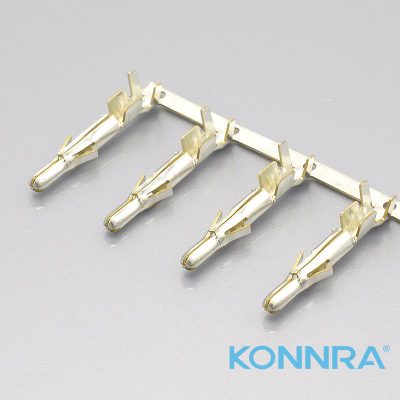
Flexibility
In more advanced interconnect designs, it becomes increasingly important for designers to have flexibility in configuring connectors. However, the ease of field replacement and maintenance of connectors is a reflection of flexibility. For applications requiring optimal environmental protection or PCB crimping, gold-plated housings and contacts are often the right choice for connector design. Because the outer shell and internal contacts are plated separately in interconnect systems, design engineers can choose tin-plated, tin/lead, gold or silver contacts based on cost and flexibility considerations.
Connectors with flexible interconnect patterns allow for the selection of higher or lower contact force contacts for most mating lead sizes. For example, in one system, 32 of the 39 contacts had at least one alternative force option. However, for applications such as high pin count interconnects, low contact forces are required and delicate, soft and flexible leads are required.
Conversely, higher contact forces are required when the connector design needs to face strong applications such as high shock and vibration, fretting corrosion, high current connections, and long-term static connections. Connectors with greater contact force help overcome oxides caused by environmental conditions, which is especially beneficial in low-current circuits.