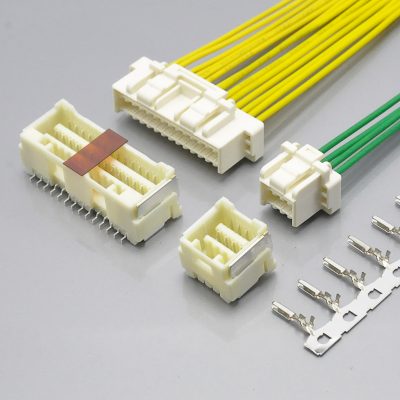
The selection of connector materials is also very different in different usage scenarios. The housing connector, as the main component of the entire connector, roughly determines the size and size of the connector. Next, we will introduce several types of connector plastic materials, which contain very important technical knowledge that all buyers, engineers, and businesses need to know.
Ⅰ. Commonly used materials for connector insulators
Usually there are: PBT, NYLON, ABS, PC, LCP and other materials, but in principle, materials with better flame resistance are used.
A.PBT material:
Generally, PBT material is added with 20-30% glass fiber, which has the ability to resist cracking, impact, and electricity. It has good wear resistance, low friction coefficient, good self-lubricating effect, and good oil and chemical resistance. It has good dielectric strength under high temperature and high humidity. Its shrinkage rate is between 0.6% and 3.0%, and its temperature resistance is about 230°C. Good formability and flame resistance. It is a commonly used rubber material for connector products.
B.NYLON66, NYLON6T
Nylon has good toughness, self-lubrication, chemical resistance, and wear resistance. PA6T has better toughness than PA9T, with a heat deformation temperature of 290 degrees Celsius, making it very suitable for SMT connectors. PA46 connector products have high strength, good toughness and are not prone to cracks.
- ABS material
It has good impact toughness, oil resistance, wear resistance, easy molding, good hardness, good rigidity, and temperature resistance of about 100°C. It is generally used in auxiliary products in connectors.
D.LCP
LCP, liquid crystal polymer, is a material with very good electrical insulation properties. It can continuously maintain its electrical properties at 200 to 300 degrees Celsius without being affected, and can reach a temperature of 316 degrees Celsius with intermittent use.
In addition, LCP connector has very strong corrosion resistance and will not be subject to any corrosion in 90% acidic or 50% alkaline environments. LCP connector also has excellent thermal stability, heat resistance, and chemical resistance.
Ⅱ. Selection Principles
- Good fluidity (such as LCP, nylon, etc., which can prepare thin-walled products)
- High strength and good impact performance
- High temperature resistance (especially SMT)
- Excellent electrical properties (high resistance, low dielectric loss)
- Short molding cycle (improve production efficiency and reduce costs)
- When the performance is satisfactory, the price is advantageous
Ⅲ. Composition and performance of connector contacts
Joint material: The metal joint material of the plug is generally brass. However, when the number of plugging and unplugging is extremely high and the life span is long, phosphor bronze, beryllium copper, etc. can also be used. The following is an introduction to the current types and characteristics of copper materials in the industry.
- Brass – an alloy of copper and zinc. The color varies depending on the zinc content.
a. Brass – containing 25~35% zinc is most suitable for processing at room temperature.
b. Brass – containing 35% to 45% tin, it is most suitable for normal temperature processing. All copper plates and copper rods sold on the market belong to this type.
- Bronze – an alloy of copper and tin, its color varies depending on the tin content.
Generally speaking, copper alloys other than brass are called bronze.
Phosphorus Bronze – Adding phosphorus to bronze has friction resistance, but too much phosphorus will make casting difficult. Its composition is 8~129% tin and 0.5~1.5% phosphorus. .
- Selection of contact material
Contacts can be made of any of several alloys, and the specific selection depends on the type of contact, the frequency of plugging and unplugging, and the electrical and environmental conditions in which the connector operates. Some commonly used materials and their applications are as follows:
Brass – Although brass is a material with good electrical conductivity, it is prone to deformation and rapid fatigue after repeated bending. It is usually used as a fixed contact in a cheap connector, or as other metal parts in the connector. Connectors with brass contacts should not be used where excellent flexibility is required. Of course, due to its low cost, brass can still be used competently as a contact in many places.
Phosphor Bronze – Phosphor bronze is harder than brass while maintaining elasticity for a longer period of time. It is often used as a contact material for operating temperatures below 300°C. For most connectors where the frequency of plugging and unplugging is low, or the contacts are in normal bends, the use of phosphor bronze can ensure good reliability.
Beryllium Bronze – Beryllium bronze has far better mechanical properties than brass or phosphor bronze. Beryllium bronze parts can be shaped and hardened after annealing, retaining their shape virtually permanently. It is also the most resistant material to mechanical fatigue. In applications where plugging and unplugging are frequent and high reliability is required, it is recommended to use beryllium bronze material.
Ⅳ. Partial plating of copper sheets
Surface processing (electroplating) of joints: In order to prevent corrosion and oxidation, smooth the contact surface and ensure the mechanical properties of raw materials, the surface of joints is generally electroplated, with various electroplating characteristics.
(1). The gold plating thickness is 30μ”, and the Ni thickness in the gold plating area is 50~80μ°.
(2). The gold plating thickness is 3μ”, and the Ni thickness in the gold plating area is 30~50μ”.
(3) Others:
Size: Acceptance based on size of order material number.
Exterior:
a. Unplated surface: no oil stains, the tape is smooth and cannot be deformed, bent or stretched.
b. Electroplating surface: smooth gloss, fine particles, no pollution and deformation.
c. Heat resistance: 85+2*C*2hr.
(4).Tinning copper sheets
a. Salt spray test shall be subject to mutual agreement.
b. The baking test is as follows (-3 items) and the tin content is less than 90%.
c. Direct tin dipping accounts for more than 90%.
d. Heat resistance: 85+2*C*2hr.
e. The copper base is plated with thick copper plating of 30~50μ°.
f. Tin-lead ratio Sn/Pb90: 10 or 95: 5