Connectors are a component that our electronic engineering technicians come into contact with frequently. Its function is to establish a communication bridge between blocked or isolated circuits in the circuit, so that current can flow and the circuit can achieve its expected function. Connectors are an indispensable part of electronic equipment. If you follow the path where the current flows, you can always find one or more connectors. Connector forms and structures are constantly changing. There are various forms of connectors depending on the application object, frequency, power, application environment, etc.
But no matter what kind of connector it is, it must ensure that the current flows smoothly, continuously and reliably. Generally speaking, what a connector connects is not limited to electrical current. Today, with the rapid development of optoelectronic technology, light is the carrier of signal transmission in optical fiber systems. Glass and plastic have replaced wires in ordinary circuits, but optical signal connectors are also used in paths and they serve the same function as circuit connectors. It can be seen that the reliability of the connector is very important. If the performance indicators of the connector cannot meet the relevant expectations, a series of problems will extend in the future, which will have various impacts on your application.
Connector reliability considers the following factors:.
- Connector product design and product manufacturing materials.
- Working environment.
- Functional requirements The application environment, especially temperature, humidity, corrosiveness, etc., determines which of its own failure mechanisms will work. The functional requirements of the connectordetermine what degree of failure is allowed.
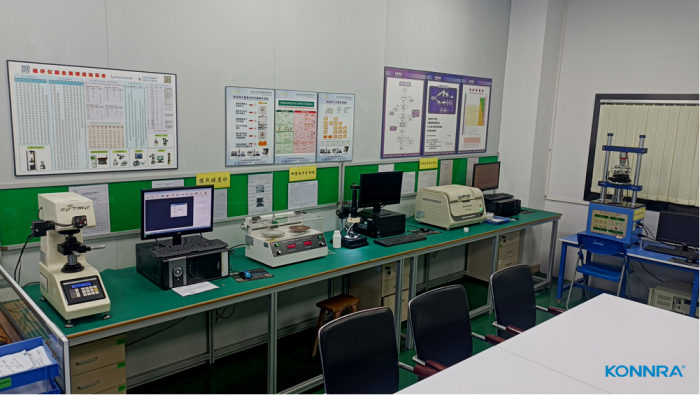
In order to understand the reliability of the connector, various tests are generally performed on the connector. The tests generally involve the following items: insertion and extraction force tests, durability tests, insulation resistance tests, vibration tests, mechanical shock tests, hot and cold shock tests, mixed gas corrosion tests, etc. The specific test items are as follows:
(1) Insertion and extraction force test.
Purpose: To check whether the insertion force and extraction force of the connector meet the product specifications.
Principle: Fully insert or pull out the connector at a specified rate, and record the corresponding force value.
(2) Durability test.
Purpose: To evaluate the impact of repeated plugging and unplugging on the connector and simulate the plugging and unplugging conditions of the connector in actual use.
Principle: Continuously plug and unplug the connector at a specified rate until the specified number of times is reached.
(3) Insulation resistance test.
Purpose: To verify whether the insulation performance of the connector meets the circuit design requirements or whether its resistance meets the relevant technical conditions when it is subjected to environmental stress such as high temperature and humidity.
Principle: Applying voltage to the insulating part of the connector will cause leakage current to occur on or within the insulating part, thereby generating a resistance value.
(4) Withstand voltage test.
Purpose: To verify whether the connector can operate safely at rated voltage and withstand overpotential, thereby evaluating whether the connector insulation material or insulation gap is suitable. Principle: Apply the specified voltage between the connector contacts and between the contacts and the shell and maintain it for the specified time, and observe whether there is breakdown or discharge in the sample.
(5) Contact resistance test.
Purpose: To verify the principle of the resistance value generated when the current passes through the contact surface: by passing the specified current through the connector and measuring the voltage drop at both ends of the connector, the resistance value is obtained.
(6) Vibration test:
Purpose: To verify the effect of vibration on the performance of electrical connectors and their components.
Vibration type: random vibration, sinusoidal vibration.
(7) Mechanical impact test.
Purpose: To verify the impact resistance of connectors and their components or to evaluate whether their structure is solid.
Test waveform: half sine wave, square wave.
(8) Hot and cold shock test.
Purpose: To evaluate the impact of connectors on their functional quality under rapid and large temperature changes. (9) Temperature and humidity combined cycle test.
Purpose: To evaluate the impact on connector performance after storage in high temperature and high humidity environments.
(10) High temperature test.
Purpose: To evaluate whether the terminal and insulator properties of a connector change after being exposed to a high temperature environment for a specified period of time.
(11) Salt spray test.
Purpose: To evaluate the salt spray corrosion resistance of connectors, terminals and coatings.
(12) Mixed gas corrosion test.
Purpose: To evaluate the corrosion resistance of connectors exposed to mixed gases of different concentrations and its impact on performance.
Environmental reliability testing equipment.
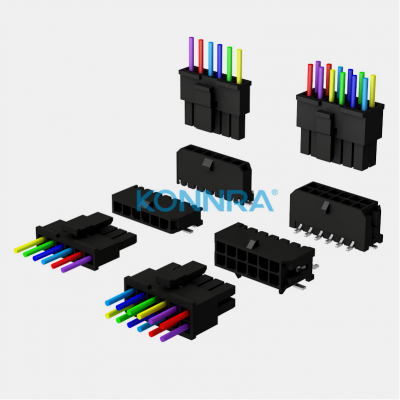
Environmental reliability testing equipment is widely used in constant temperature, constant humidity, changing temperature, changing temperature and humidity, and salt spray tests on raw materials, component levels, circuit board/module levels, and complete electronics, electrical appliances, electricity and other products. Mixed gas test, ozone aging test, UV accelerated aging test, xenon lamp aging test, sulfur dioxide corrosion test, high altitude low pressure test, IPX1~8 waterproof grade test, dust/sand dust test, drop test, combustion test, half sine wave /Trapezoidal wave acceleration impact test, sine/random vibration test, collision simulation test, drop test, tensile strength test, fatigue test, seismic test, highly accelerated life aging and stress screening and other mechanical and mechanical environment tests, climate environment test and comprehensive Environmental testing project.