What are the factors causing corrosion of male and female connectors?
The male and female headers are the first parts of the connector that come into contact with the circuit. They are usually made of metal and are the core components of the connector, making direct contact and transmitting current. Corrosion of male and female connectors means that the metal part of the connector is damaged by chemical or electrochemical reactions, resulting in the performance degradation or failure of the connector, which will have a severe impact on the connector and even endanger the end product.
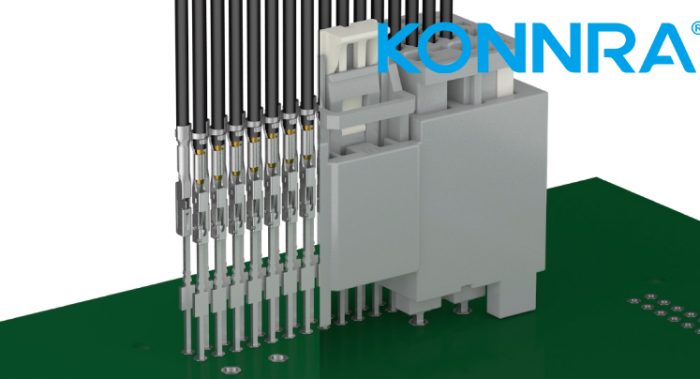
- Caused by oxidation or galvanizing
When the metal in the connector reacts with oxygen in the surrounding air, metal oxides form, triggering oxidation. These oxides can hinder the flow of current, making the connector susceptible to environmental influences and electrical corrosion. Zinc plating is a method used to protect metal surfaces, but if the plating is uneven or damaged, it can also cause the metal of the connector to be exposed to air, causing oxidation. Therefore, it is important to regularly check the status of the connector. Once severe oxidation is detected, immediate replacement is a key step to ensure safe operation of the equipment.
2.Electric corrosion
Under harsh environmental conditions, the action of electric current causes different metals to release or absorb electrons in the presence of electrolytes, causing the metal materials to gradually dissolve. Weakening the metal part of the connector, damaging its original structure and electrical conductivity, ultimately leading to functional impairment or even complete failure of the connector.
- Corrosion of liquid
Although many male and female connectors are designed for harsh environments, corrosion often shortens their service life. Gaps and other leakage paths in wires, insulation, plastic housings and pins can easily soak in water and other liquids, accelerating the corrosion of male and female connectors.
- Other factors
The lubricants and coolants that keep automated assembly lines running can corrode plastic insulation. Likewise, the steam and corrosive chemicals used to flush some food processing equipment can severely damage connector continuity.
This shows that corrosion not only causes serious damage to connectors, but also affects the reliability and normal use of smart devices. In order to prevent corrosion problems of male and female connectors, routine maintenance and timely replacement are very important. At the same time, choosing connectors with high protection levels can also more effectively prevent liquid and dust erosion, making the use of smart devices more stable and reliable.
Therefore, in order to make the male and female connectors last longer and maintain better performance, it is crucial to be dust-proof, waterproof, anti-corrosion and durable.
Konnra Electronics’ product series has these characteristics. It has passed the authoritative certification of UL laboratory and is silver-plated, which greatly improves the conductivity and corrosion resistance of the connector. In addition, it also has a hidden buckle and safety locking TPA device and CPA device design. This unique improved design allows cars, drones and other equipment to be used without worrying about the vibration causing the plug to fall off. Improved security.