Connectors are an integral part of communication equipment, and looking along a current path, you can always find one or more connectors.
In the circuit is blocked or between independent circuits to establish a communication bridge, so that the flow of current, so that the circuit to achieve the function required by the designer.
Connector wiring method, professionally known as termination method, refers to the way the contact surface of the connector is connected to the cable wires. In order to meet the diverse requirements of connection methods in long-term use, such as robustness, reliability, convenience, etc., the designer will design or select a reasonable termination method according to the usage scenario and working conditions.
Common termination methods:
Proper selection of termination methods and proper use of termination techniques are important aspects of extending connector life and holding power. There are several common connection methods:
1, Welding, also known as fusion, is a manufacturing process and technology to join metals or other thermoplastic materials, such as plastics, by means of heat, high temperature or high pressure.
Welding is the process of joining two or more materials, identical or dissimilar, through the bonding and diffusion of atoms or molecules. The bonding and diffusion of atoms and molecules is facilitated by heat or pressure, or both. Welding is accomplished by fusion welding, pressure welding, and brazing.
The most common type of soldering is tin soldering. For soldered connections, it is of utmost importance that metallic continuity should be formed between the solder and the surface to be soldered. Therefore for connectors, solderability is important. Tin alloys, silver and gold are the most common platings on the soldered end of connectors.
2, Crimping, an emerging technology that replaces soldering technology, provides a low-cost, high-quality connection between terminals and wires. A good crimp connection produces a mutual fusion flow of metals, causing symmetrical deformation of the wire and contact to the material. This connection is similar to a cold welded connection and gives better mechanical strength and electrical continuity and can withstand harsher environmental conditions. Currently, it is generally accepted that a properly crimped connection is better than a soldered one, especially in high-current applications, where crimping must be used. For crimping, special crimping pliers or automatic or semi-automatic crimping machines must be used. Depending on the cross-section of the conductor, the correct wire crimp pair should be selected. Note that crimped connections are permanent connections and can only be used once.
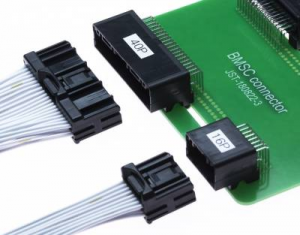
3, Wrapped connection, is to wrap the wire directly on the contactor winding column with prongs. wrapped connection, the wire in the force is controlled by the winding, pressed into and fixed in the prongs of the contact winding column, in order to form a gas-tight contact. Wrapping requires the use of a tool such as a winding gun or stationary winding machine. This type of termination is rarely used in low voltage connectors.
4, Pierced connection, also known as insulation displacement connection, applicable to the connection of ribbon cable, the connection does not have to strip the cable insulation, the connector’s U-type contact spring tip penetrates the insulation, so that the cable conductor slides into the groove of the contact spring and is clamped, so that the cable conductor and the connector spring to form a tight electrical connection between the cable conductor and the connector. It is a novel termination technology invented by the U.S. in the 1960s with high reliability, low cost, ease of use and other features, and has been widely used in a variety of printed board connectors.
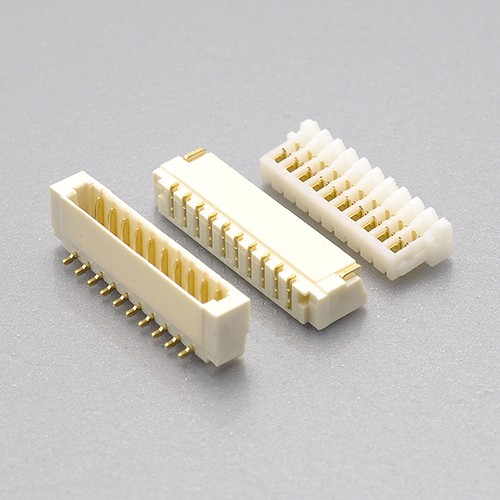
KR0800 Series SUR IDC Connector is suitable for dense electronic equipment, can be omitted from the soldering process, the wire stripped off the outer cover and then directly into the riveting pressure can be.
5, Screw connection, is the use of screw terminal connection method. The use of the maximum and minimum cross-section of the connecting wires and different specifications of the screws allow the maximum tightening torque.
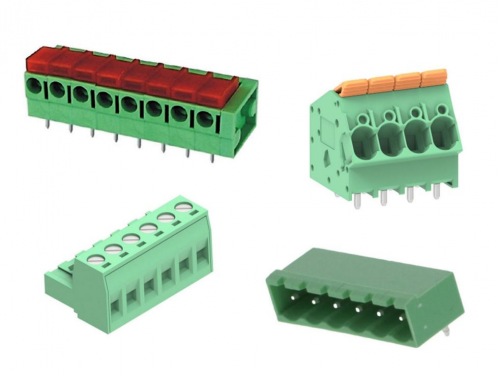
How to choose the termination method of low voltage connectors
The above five connector methods are currently commonly used in the market for low-voltage connectors are piercing, crimping and soldering.
First, the environment needs to be considered. If the spatial environment where the low voltage connector is located is well controlled and does not require frequent movement, then crimp connectors can be very effective as long as they are assembled with the proper tools.
However, in more hostile environments, soldered and pierced connectors should be used to provide a more reliable connection.
Other considerations should include power (current or RF) and frequency. Higher power connections will be subjected to greater heating stress due to the higher resistance inherent in crimp connections. There are scenarios where the number of times a connector can be reused also needs to be taken into account, in which case a piercing connection is not applicable.
In practice, soldered connections are more versatile, while crimped connections are more convenient and effective and save time and costs, and pierced connections have a longer retention force. If you have doubts about the termination method or if you need a connector, you can contact KONNRA for a customized solution for your system.