Connectors can be found everywhere in real life, and they are integrated into every aspect of our lives in many ways. The most intuitive example is our frequent use of mobile phone connectors and USB connectors, these essential components of consumer electronics products, almost every day with our close contact. In addition, there are many connectors are quietly behind the scenes to play a key role, such as Board-to-Board connectors and FPC connectors, etc., they are not often directly exposed to the line of sight, but many devices are indispensable to connect the internal bridge. Although there are many types of electronic connectors, but their manufacturing process is basically the same, generally can be divided into: Stamping, Plating, Molding, Assembly, the four stages, the following to explain in detail the process of the four manufacturing stages.
Ⅰ. The connector production of the pre-process
1, material procurement: in the initial stage of connector manufacturing, the first task is to carry out the procurement of raw materials. Generally speaking, the construction of the connector is a precise blend of plastics, metal parts and springs and other core materials. In view of this, ensuring that the selected materials are of excellent quality and precise specifications is decisive for the optimisation of the final product’s performance and quality assurance. This process is not only about the materials themselves, but also about the overall quality control of the connector. How to select different materials can be seen before the release of the article – Connector Popular Science|Connector insulator commonly used materials and characteristics of introduction.
2, design mould: the design of the mould is one of the important links in the production of connectors. The precision and stability of the mould directly affects the precision and stability of the product.
Ⅱ. The connector processing process
1, stamping
The manufacturing process for electronic connectors generally begins with the stamping of pins. Stamping covers a variety of sheet metal forming manufacturing processes, using mechanical presses or stamping machines for punching, dropping, embossing, bending, flanging and embossing. At KONNRA Connectors, thin metal strips are stamped into connector pins using large, high-speed stamping presses. One end of the large roll of metal strip is fed into the front end of the press, and the other end is wrapped around the hydraulic table of the press into the reeling wheel, which pulls out the metal strip and rolls it up to stamp out the finished terminals.
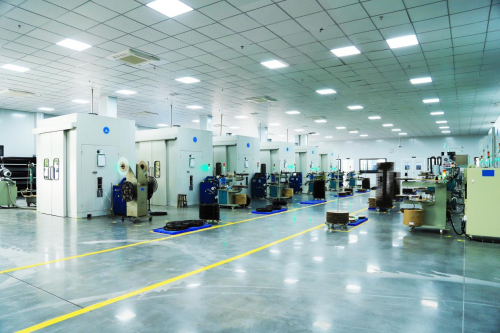
2, Electroplating
After stamping is completed, the connector pins will be sent to the plating stage. In this stage, the electronic contact surface of the connector will be plated with various metal coatings, such as nickel plating, tin plating, half gold plating, etc., to prevent oxidation and strengthen the conductivity. Twisting, chipping or deformation of the pins may occur during the plating process, but these quality defects are easily detected by technical inspection.
3, Injection Moulding
Plastic cassettes for electronic connectors are made in the injection moulding stage. Connector injection moulding is usually the process of melting plastic into the metal tyre film, and then quickly cooled to form. When the melted plastic is not completely filled with the tyre film when the so-called short shots, this is the injection stage needs to detect a typical defect.
Other defects include filled or partially blocked sockets (which must be kept clean and unobstructed in order to be properly connected to the pins during final assembly). Given the efficiency of the backlighting technique, it shows significant advantages in detecting missing cassettes and blocked jacks after the connector has been injection moulded. This makes the design of machine vision systems for connector quality control relatively straightforward and easy to implement, ensuring a streamlined and efficient inspection process.
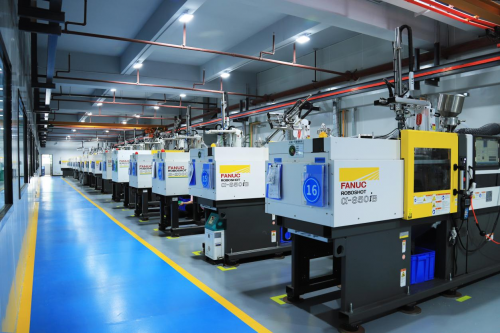
4, Assembly
This is the final stage of connector manufacturing, the electroplated pins and injection moulded box seat plug assembly. There are two types of assembly: individual pairs of pairs of pairs of pairs of pairs of pairs of pairs of pairs of pairs of pairs of pairs. Individual pairs of insertion refers to the insertion of a pin each time, while the combination of pairs of insertion is a number of pins at the same time with the box seat insertion.
Regardless of the method of assembly, it is important to ensure that all pins are not missing and are correctly positioned. KONNRA connectors are mechanically assembled to minimise the errors that inevitably occur with manual assembly.
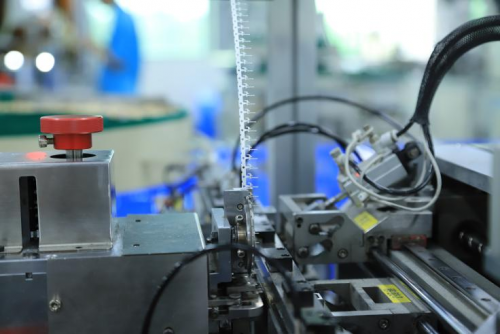
Ⅲ. The connector inspection process
KONNRA connector has achieved 95% of the full-intelligent visual CCD inspection coverage, the use of imported “Mitsubishi Panasonic” PLC control system, FA25-35mm optical lens, 5 megapixel camera, equipped with advanced visual inspection software, a better alternative to manual visual inspection. The core function of this equipment focuses on the comprehensive inspection of product defects, covering multiple dimensions such as crack identification, deformation assessment, foreign object detection, dirt analysis and defect determination. At the same time, it has precise measurement capabilities for quantitative analysis of dimensions, pitches and angles; in terms of positioning, it can accurately confirm the position, direction and rotation of the product. In addition, it has powerful recognition capabilities to identify multiple information such as shape features, colour attributes, texture details and edge contours of the product. It replaces heavy and monotonous manual inspection work and improves productivity and accuracy.
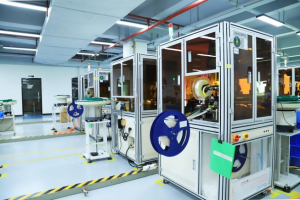
Connector production process requires close co-operation between various links, strict control of each detail to ensure that the connector quality and performance to meet customer requirements. At the same time, continuous improvement of process technology and production equipment, improve production efficiency and product quality is the key to the connector production process.KONNRA connectors in the connector market has more than 20 years of experience precipitation, the most advanced equipment configuration, all-round control of the production of the product, to the customer to hand over a satisfactory answer sheet.