As with most electronic components, the connector components and the quality of processes directly affects the quality and performance of the finished product. For PCB connectors, these factors include pin material, type of plastic, quality of molded plastic body, quality of surface finish (plating), manufacturing/assembly process, and packaging.
Electroplated coatings are vital to the manufacture of electronic components, and this is also true for connectors. It contributes to the performance, utility and durability of the product. Proper coatings help ensure reliable operation of equipment. Plating improves corrosion resistance and electrical conductivity. It enhances connector solderability and protects metal conductors from abrasion. But which material should be used for plated connector pins and electrical contacts?
Learn more about plating metals for connector pins and contacts. Can assist you in finding the right material for your application.
I. Precious Metals
Connector pins and electrical contacts have a variety of plating options. Precious metals are ideal because they lack chemical reactivity and are resistant to oxidation and corrosion.
1. Gold is one of the most popular choices in electroplating. Gold has strong electrical conductivity even at low voltage. Compared to other metal coatings, gold is highly resistant to oxidation and corrosion.
Gold is particularly suitable for high humidity or frequent thermal cycling. It is particularly suitable for flexible connections and spring coatings. Gold is not magnetic, so it is particularly suitable for medical devices such as MRI scanners.
The main disadvantage of gold is its high price. Gold is expensive compared to other options. Common plating thickness: 10-50 u”
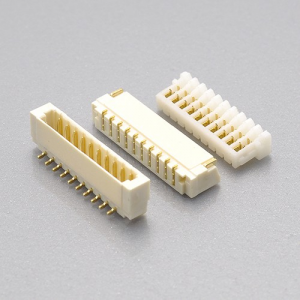
KR0800 Series SUR IDC Connector is gold-plated. The combination of lightweight design construction and gold-plating makes it more suitable for dense electronic equipment.
2. Silver is another option for highly conductive coatings. It has good corrosion resistance. Silver is cheaper than gold and performs well in high power power transmission applications. Due to its low cost, it is preferred for large components. Silver is a metallic lubricant and is particularly well suited for threaded or sliding contacts.
The main disadvantage of silver plating is that it oxidizes to produce compounds such as silver sulfide, which reduces conductivity. Common coating thicknesses:100-300 u”
3. Palladium is highly resistant to corrosion and has high electrical and thermal conductivity. It is harder than gold and silver. This strength makes it ideal for highly wear-resistant applications. Palladium’s low surface circuit resistance makes it particularly suitable for plating connectors and contacts. Common coating thicknesses:10-30 u”
4. Rhodium is harder than palladium. It is highly conductive and very resistant to corrosion and acids. It is well suited for applications requiring good wear resistance and high hardness. Common plating thickness: 20 u”
II. Inert metals
Inert metals are non-precious metals with high corrosion resistance. The oxide layer forms a thin film on the surface of the metal, which prevents further corrosion.
1. Tin has some corrosion resistance. It is non-toxic in lead-free construction, which is advantageous for medical applications. Only some older military programs still require the use of leaded tin.
Tin has low contact resistance and good solderability. It is a low cost option.
Tin is best suited for applications with relatively few mating cycles. It performs well in dry circuits and under low voltage conditions. However, it is not suitable for sustained use at high temperatures. Common plating thickness: 100-300 u”
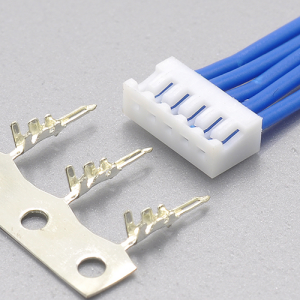
KR1252 Series Board In Connector is tin-plated and is suitable for the connection of devices in the medical field.
2.Nickel is very hard and durable, resistant to wear and tear and very corrosion resistant, and has high electrical conductivity. Because of its durability, nickel is ideal for frequency pull-out parts.
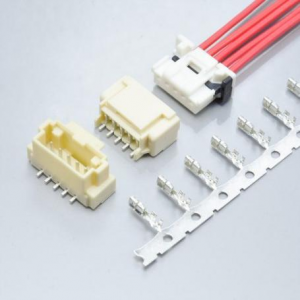
KR2017 Series Duraclik 2.0 Wire to Board TPA Connector plating options of nickel plated matte tin with TPA latch design can be applied in high frequency vibration and high temperature environments with excellent electrical contact reliability.
III. Other types of metals
There are other plating metals available. However, they are prone to corrosion and are usually not applied separately in product plating.
Copper is one of the materials with the highest electrical conductivity, making it a cost-effective solution. However, it is not usually used alone and must have a protective layer to prevent corrosion.
Copper is usually the substrate for metal plating, has excellent adhesion and is suitable for enhancing the adhesion between coatings. Copper performs best in a relatively stable, dry environment.
IV. Metal alloys
Metal alloys are a very common choice in the market. Alloys combine metals with other metallic or non-metallic materials to increase plating optionality.
1. White bronze is an alloy of copper, tin and zinc, non-magnetic, it has better conductivity than nickel. It has good resistance to wear, corrosion and rust. Ideal for medical connector applications. It is well suited for RF connectors. It performs well in environments with rapid temperature changes. Common plating thickness: 50-200 u”
2. Palladium-nickel alloys were originally introduced as a low-cost alternative to gold. The alloy has very good corrosion resistance, low contact resistance and good solderability. It is heat and pressure resistant. Palladium-nickel is usually plated with gold. This gives it lubricating properties and better corrosion resistance.
Palladium-nickel can withstand a large number of insertions and withdrawals. It is ideal for applications that require durability and lighter weight. It performs well in high temperature environments. Common plating thickness: 10-30 u”
3. Electroless nickel plating is versatile and can be applied to both conductive and non-conductive surfaces. This nickel alloy coating is deposited by chemical reduction, which means that, unlike nickel plating, it does not require an electric current.
Most electroless nickel coatings contain 2-14% phosphorus. The higher the phosphorus content, the better the corrosion resistance, but the hardness is reduced.
Compared to electrolytic nickel, chemical nickel plating provides a more uniform thickness on the substrate, even in holes and internal diameters. Chemical nickel plating is also less prone to porosity.
4. Nickel-phosphorus alloys have high wear and corrosion resistance. They have good solderability and provide some lubrication. Nickel-phosphorus forms uniform layers of varying thickness and is commonly used for chemical plating. This process is an alternative to electroplating. It uses a chemical process rather than an electric current to deposit the alloy.
Nickel-phosphorus is a good choice for parts that are difficult to coat. It performs well in corrosive environments. It can handle high-use applications. Common plating thickness: 1-40 u”
How to choose the right contact plating for connector pins
Connector pins and contacts are available in a variety of coating options. How you choose depends on what kind of performance you need for your project and your budget.
KONNRA connector experts can help you find the right connector solution for your project. KONNRA Connectors has years of experience in connector manufacturing and we will help you find the perfect connector for your project.