Welcome to the world of Konnra! Here, we provide you with a comprehensive guide on snow sweeper wiring harnesses. With over 20 years of experience as a manufacturer of electronic connectors and wiring harnesses, we are dedicated to creating maximum value for our customers. Our mission is to help you solve any technical challenges through high-quality products and unparalleled engineering support. In this article, we will delve into the functions and design of snow sweeper wiring harnesses, helping you fully understand the importance of these critical components during harsh winter conditions. We will share how to properly install and maintain the harnesses, ensuring your equipment operates reliably in the worst weather conditions. We hope this article provides you with practical knowledge and valuable insights.
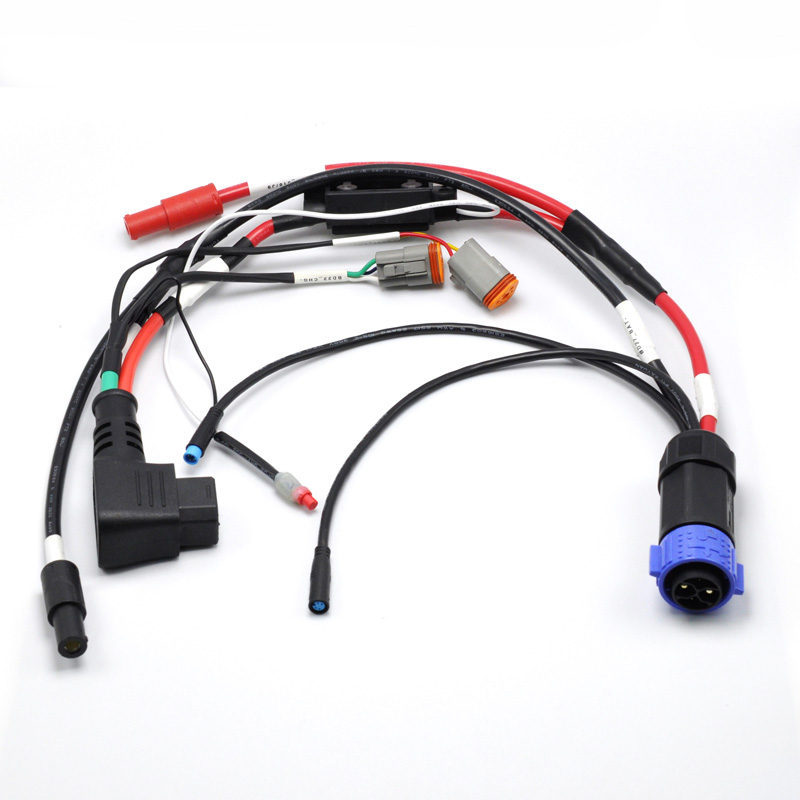
1. Basics of Snow Sweeper Wiring Harness
1.1 What is a Wiring Harness?
A wiring harness is an organized set of wires, terminals, and connectors that run throughout a vehicle, transmitting electrical power and signals to various systems and components. In snow sweepers, the wiring harness is vital for connecting the electrical and electronic parts, ensuring they work together seamlessly.
1.2 Components of a Wiring Harness
Wires: The core element, typically made of copper or aluminum, that carries electrical current. The choice of wire material affects the conductivity, flexibility, and durability of the harness.
Connectors: These join different parts of the harness, allowing for modular replacements and repairs. Connectors must be durable and able to withstand the harsh conditions snow sweepers operate in.
Insulation Materials: Protect the wires from moisture, chemicals, and physical damage. Insulation materials must be chosen to provide adequate protection against the extreme cold and wet conditions typical of snow sweeping operations.
1.3 Role in Snow Sweepers
In snow sweepers, the wiring harness is crucial for:
Powering the Engine and Other Electrical Components: The wiring harness delivers the necessary power to start the engine, operate lights, and run various accessories.
Connecting Control Units and Sensors: Ensuring the seamless operation of control systems and sensors that monitor the snow sweeper’s performance and environmental conditions.
Managing Lighting Systems and Other Safety Features: Ensuring the reliability of lighting systems, which are essential for visibility and safety during snow clearing operations.
2. Design and Manufacturing of Snow Sweeper Wiring Harness
2.1 Design Principles
Designing a wiring harness for snow sweepers involves several critical considerations:
Cold Resistance: The harness must operate efficiently in low temperatures, which means using materials that remain flexible and conductive even when cold.
Waterproofing: Protecting the harness from snow and moisture is essential to prevent short circuits and corrosion.
Durability: Using robust materials to withstand constant vibration, mechanical stress, and exposure to harsh chemicals, ensuring a long service life.
2.2 Material Selection
Wires: Copper and aluminum are commonly used due to their excellent conductivity. Copper is preferred for its superior conductivity and flexibility, while aluminum offers a lighter weight.
Insulation: PVC, rubber, and advanced polymers are chosen for their insulating properties and ability to withstand cold temperatures. These materials protect the wires from environmental damage and ensure electrical safety.
Connectors: Made from corrosion-resistant metals or high-strength plastics, connectors must provide reliable electrical connections and resist environmental degradation.
2.3 Manufacturing Process
Wire Processing: Cutting, stripping, and crimping wires to the desired length and specifications. This process must be precise to ensure the reliability of the final product.
Assembly: Combining wires, connectors, and insulation into a complete harness. This involves routing the wires through protective sleeves and securing them with clips or ties.
Quality Control: Conducting rigorous tests to ensure the harness meets performance and safety standards. This includes checking for continuity, insulation resistance, and the overall integrity of the harness.
2.4 Performance Testing and Certification
Cold Endurance Tests: Verifying the harness functions at sub-zero temperatures. This ensures that the materials and connections do not become brittle or fail in cold conditions.
Voltage Testing: Ensuring the harness can handle the required electrical load without failure. This includes tests for current-carrying capacity and voltage drop.
Certifications: Complying with industry standards such as ISO and UL to guarantee quality and safety. These certifications demonstrate that the harness has been independently tested and meets stringent quality requirements.
3. Installation and Maintenance of Snow Sweeper Wiring Harness
3.1 Installation Steps
Preparation: Gather necessary tools and materials. This includes wire strippers, crimping tools, connectors, and protective sleeves.
Routing: Lay out the harness along the intended path, avoiding sharp edges and heat sources. Proper routing is crucial to prevent damage and ensure the harness is secure.
Connecting: Secure connectors to the corresponding components, ensuring firm and accurate connections. It is important to follow the manufacturer’s instructions to avoid incorrect connections.
Final Check: Test the system to ensure all components function correctly. This includes checking for proper voltage and continuity in all circuits.
3.2 Common Issues and Solutions
Poor Connections: Can lead to intermittent failures. Ensure all connectors are firmly attached and inspect them regularly for signs of wear or corrosion.
Wire Damage: Regular inspection and protective coverings can prevent wear and tear. Look for signs of abrasion, cuts, or other physical damage.
Short Circuits: Proper insulation and waterproofing techniques help prevent moisture-related issues. Regularly check for signs of moisture ingress and address any issues promptly.
3.3 Maintenance Tips
Regular Inspections: Check for signs of wear, corrosion, or damage. Inspect the harness at regular intervals to catch issues early.
Cleaning: Keep connectors and wires free from dirt and debris. Use appropriate cleaning solutions and methods to avoid damaging the components.
Protective Measures: Use sealants and protective covers to enhance durability. Apply protective coatings to exposed connectors and wires to prevent corrosion.
4. Innovations and Future Developments in Snow Sweeper Wiring Harness
4.1 New Material Applications
High-Strength Alloys: Improve the robustness of wires and connectors. These materials offer better resistance to mechanical stress and environmental factors.
Nanomaterials: Enhance conductivity and resistance to environmental factors. Nanotechnology can provide superior performance characteristics, including better flexibility and higher strength.
4.2 Smart Wiring Harnesses
Self-Diagnosing Harnesses: Equipped with sensors to monitor performance and detect faults. These harnesses can provide real-time feedback on their condition, allowing for proactive maintenance.
Integrated Sensors: Provide additional data and functionality, such as temperature and humidity monitoring. This can help optimize the performance of the snow sweeper and improve safety.
4.3 Environmental and Sustainability Considerations
Recyclable Materials: Reduce environmental impact by using materials that can be reused. This helps minimize waste and supports sustainable practices.
Energy-Efficient Manufacturing: Implement processes that consume less energy and produce minimal waste. This includes using renewable energy sources and adopting lean manufacturing techniques.
4.4 Future Trends
Automation and Smart Technology: Increased use of automation in design and manufacturing. This can improve the accuracy and efficiency of wiring harness production.
Market Demand and Innovation: Rising demand for more efficient, durable, and intelligent wiring harnesses. Innovations in materials and design are driven by the need for better performance and reliability.
Conclusion
In conclusion, the snow sweeper wiring harness is an indispensable component that ensures the reliability and efficiency of snow sweepers. From basic functions to advanced innovations, understanding the design, manufacturing, installation, and maintenance of these harnesses can significantly enhance their performance and longevity. Staying informed about the latest trends and technologies allows consumers to make better decisions and ensure their equipment operates smoothly even in the harshest conditions.
Ready to upgrade your snow sweeper’s performance? Visit Konnra’s website to explore our high-quality snow sweeper wiring harnesses and other electronic connector solutions. Discover how our products and engineering support can make a difference in your operations. Get in touch with us today and let Konnra help you tackle the winter season with confidence!