I. Status of the technology-based electronics industry
We are in a phase of rapid technological development.Today’s electronics, with their innovative new sensors, detectors, monitors and communicators, are dominating and changing our daily lives.Designers are using high-speed circuit chips to create new products and instruments that consumers expect to run faster and last longer at levels unimaginable years ago. The development of new products of all kinds has also driven tremendous advances in the design of application connectors and components.
The application connectors that have been standardised in the current market serve as an important resource for custom connector reference designs, which are widely used to meet the needs of many consumer electronics products.However, as technology evolves to meet new and emerging needs, these standardised application connectors are showing limitations in terms of speed and size, making it difficult to meet designers’ stringent requirements for higher speeds and smaller sizes.As a result, it is often necessary to redesign and develop new connectors for specific product requirements to ensure product competitiveness and market adaptability.
Ⅱ. The application of connectors in the technology-based electronics industry application areas
VR wearable technology is one of the application areas where systems are forcing designers to use original connector designs. These small devices require smaller connectors to reduce space and weight while increasing the functionality, portability and durability of the instrument. Interconnect systems endure much of the wear and tear of plug-and-play systems that are subjected to multiple disconnect and reconnect cycles when components are replaced. Durability and secure connections are critical in wearable applications when cables are wrapped around devices or people.
Critical shifts in chip technology and higher speed digital design are significantly changing the interconnect world. The electrical performance of the interconnected world is highly dependent on the cables used and the method of connection of the connectors. While new industries of all kinds are thriving, the connector industry must also change in response to the needs of the industry.
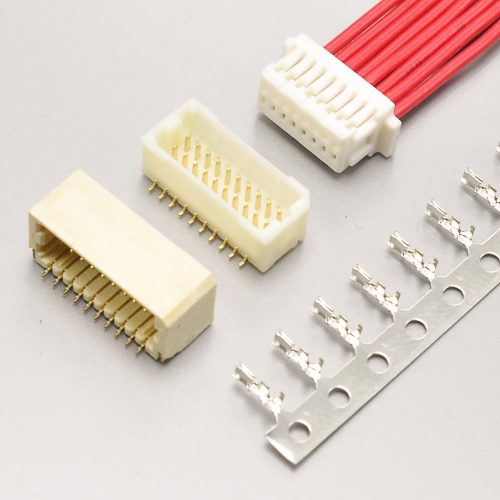
KR1000 series connector is a 1.0mm pitch connector and a dual row wire-to-board connector. Adopting plastic shell locking method, the terminal adopts centralised contact method, with high contact reliability, low profile design, to meet the equipment miniaturisation and high-density packaging needs.
In many precision systems, cables and connectors are specifically designed for the application. In the field of prosthetics, for example, one can now see disabled people operating complete robotic hands through the connection of connectors.
IMEC develops implantable chips with the world’s highest electrode density.
III.The advantages of KONNRA connectors
Custom design of connectors used to be considered expensive and time-consuming. However, KONNRA Connectors has optimised mould design, shortened sample lead times, 3D manufacturing equipment and directly connected CNC machinery through MoldFlow software and Ansys 3D software. The hardware and software equipment covers reverse analysis, R&D design, mould manufacturing and functional testing, with the ability to design independently according to market demand and tailor-made according to customer requirements.
KONNRA’s talented research and development staff can not only optimise connector designs for customers, helping them to meet customer requirements for reduced size and weight, adherence to specific form and mating parameters, but can even improve the functionality of portable electronic devices. The ability to hand over physical model drawings to designers at the beginning of the connector design process supports rapid review and approval, and after approval, it typically takes less than three to four weeks to fully assemble a new connector and its corresponding harness.
KONNRA Original Approved Connectors must undergo rigorous testing by CNAS to ensure product safety and interoperability.After confirming that the products have large-scale production capacity, KONNRA has more than 40 sets of FANUC high-precision plastic injection moulding machines, combined with advanced hot runner moulding technology, to build up a highly efficient production system. At the same time, the company has a special warehouse to store raw materials and connector finished products to ensure that the production process of high-speed response capability, which not only guarantees the stability of product quality, but also to ensure the punctuality of the delivery date. Through this series of measures, KONNRA accelerates the promotion and delivery of customers’ new technologies in the global market, and helps customers to seize the first opportunity in the market.