A、Main Categories of Industrial Automation Equipment
1.1 Industrial robots
Industrial robots are representatives of industrial automation. They usually consist of multiple degrees of freedom robotic arms and various sensors that can perform various tasks such as welding, assembly, spraying and handling.
1.2 Automated production line equipment
An automated production line is a production system composed of multiple automated equipment used to complete the manufacturing of specific products. These production lines include conveyor belts, mechanical devices, testing equipment, etc., which can greatly improve production capacity and product consistency. For example, automated production lines in the automobile manufacturing industry can assemble automobile parts in a short time and achieve efficient production.
1.3 Automated testing equipment
Automated testing equipment is another important equipment in the fully automatic production line. It can automatically detect products and achieve automated control of product quality.
There are many types of automated testing equipment. Common ones include optical testing equipment, electronic testing equipment, mechanical testing equipment, etc. Optical inspection equipment is suitable for inspecting product appearance, size, shape, etc., and has the advantages of high precision, high speed, and high reliability.
1.4 Automation control equipment
Automated control systems are used to monitor and control various parameters in industrial processes to ensure product quality and production efficiency. These systems typically include sensors, actuators, and controllers that maintain system stability through feedback loops. Automation control systems are widely used in chemical industry, electric power, manufacturing and other fields to help companies achieve precise process control and resource optimization.
B. Connectors in industrial automation equipment
With the continuous development of industrial automation, robots have ushered in huge market demand and put forward higher requirements for connectors. Facing the opportunities and challenges presented by the times, Dongguan Konnra Electronics continues to expand the application fields of interconnection solutions and has successively launched modular industrial automation system cable connectors for transmitting power and signals between controllers and robots.
For example, pcb connectors and KR2516 2.5mm pitch connectors can be designed according to applications such as industrial robot control and have excellent conductivity and small size. Stability is crucial in industrial automation connectors. KR2516 is equipped with a TPA locking device, which can ensure that the terminal is installed in place and provides locking force to the terminal to prevent the wire end and the plastic shell end from loosening.
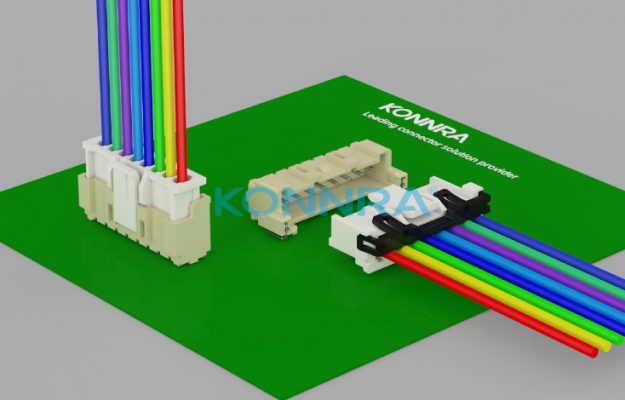
Konnra 4.2mm connectors are designed for blind mating applications. These connectors allow mismating. In hard-to-reach applications, connectors require hidden plug-in designs, which can result in damage to the connector or terminal and waste valuable man-hours. Konnra connector products help prevent end product failure by providing terminal position assurance. Reduces terminal disengagement by providing locking redundancy; unless terminals are correctly inserted, assemblers cannot install them. Konnra Electronics connector products offer compliant pin interfaces while retaining all the features of standard-fit 4.2mm connectors. This rugged “pin” design provides a reliable interface during circuit board layout. 4.2mm plastic housing connectors mate with 4.2mm wafer to allow for wiring changes when converting boards from soldering to press-fit applications. 4.2 (lower mating and unmating force) terminals are designed for applications that require lower engagement and disconnection forces or where the device is frequently mated and unmated. Pre-lubricated terminal models are rated for up to 250 mating cycles and housed in a standard 4.2mm housing. Applications often require rugged terminals and low mating and unmating forces to ease operator effort during assembly or to withstand high mating and unmating cycles.
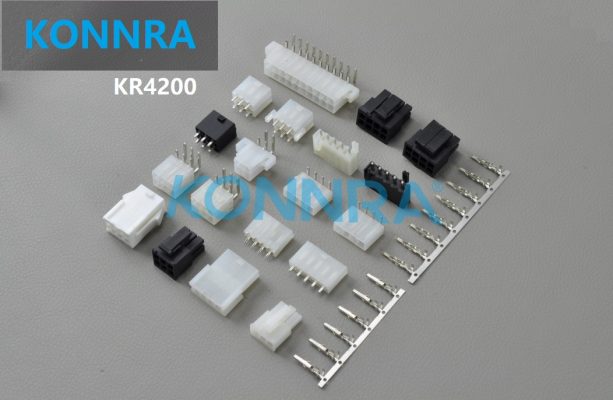
C、Industrial automation drives connector development
With the development of industrial automation, the demand for connectors is also growing. According to forecasts from market research institutions, the global industrial automation connector market will have a compound annual growth rate of 6.8% from 2020 to 2026, and the market size will reach US$14 billion by 2026. The main driving factors of the industrial automation connector market include the following:
- Promotion of Industry 4.0 and smart manufacturing. Industry 4.0 refers to the use of technologies such as the Internet of Things, cloud computing, big data, and artificial intelligence to realize the digitization, networking, and intelligence of the production process. Intelligent manufacturing refers to the use of intelligent equipment, intelligent systems and intelligent services to achieve optimization, collaboration and innovation of the production process. The application of these technologies requires a large amount of data transmission and signal exchange, thus placing higher requirements on connector performance and reliability.
- Development of new energy and electric vehicles. New energy sources and electric vehicles are important ways to combat climate change and environmental pollution. They also require a large number of connectors to achieve power conversion, storage and transmission. For example, wind turbines require connectors to connect turbine blades, generators, and transformers; solar panels require connectors to connect inverters, energy storage devices, and the grid; electric vehicles require connectors to connect battery packs, charging piles, and vehicle mounts. system.
To sum up, connectors have a broad future prospect in the field of industrial automation, and they will provide more efficient, safer, and more environmentally friendly solutions for various industries.