When it comes to keeping your electronic devices and systems running smoothly, a reliable header connector is essential. These connectors play a vital role in ensuring that signals and power flow seamlessly between components, whether in consumer electronics or heavy-duty industrial machinery. However, corrosion can be a real challenge, threatening the performance and lifespan of your connectors. That’s where Konnra comes in—we understand the importance of protecting your connectors from corrosion. In this article, we’ll dive into the causes of corrosion, the types that typically affect header connectors, and, most importantly, share strategies to prevent it. With our expertise, you’ll be well-equipped to keep your connectors in prime condition and your projects running without a hitch.
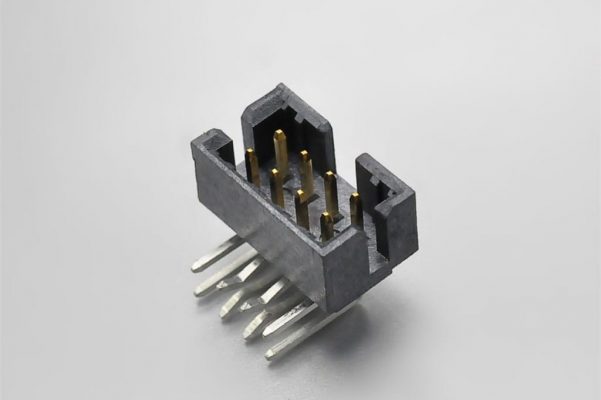
Ⅰ. Causes of Corrosion in Header Connectors
Understanding the root causes of corrosion is the first step in effectively protecting your header connectors. Corrosion occurs when metal surfaces react with environmental elements, leading to the deterioration of the material. For header connectors, several factors can contribute to this process.
Environmental Factors
Moisture and Humidity: One of the most common culprits behind corrosion is moisture. When water vapor condenses on the surface of a header connector, it can initiate the oxidation process, leading to rust and other forms of corrosion. This is particularly problematic in humid climates or areas where temperature fluctuations cause condensation.
Salt Spray and Salinity: In coastal regions or marine environments, the presence of salt in the air can greatly accelerate corrosion. Salt acts as an electrolyte, speeding up the oxidation process and causing rapid degradation of metal surfaces.
Chemical Exposure: Industrial environments often contain airborne chemicals that can react with metal connectors, leading to corrosion. Acids, alkalis, and solvents are particularly aggressive, breaking down protective coatings and exposing the metal to further damage.
Material-Related Factors
Galvanic Corrosion: This type of corrosion occurs when two dissimilar metals come into contact in the presence of an electrolyte, such as water. The more reactive metal (anode) will corrode faster, while the less reactive metal (cathode) remains relatively unaffected. This is a common issue in electronic connectors, especially when different metals are used in the same assembly.
Inadequate Protective Coatings: Header connectors are often coated with protective layers, such as nickel or gold, to prevent corrosion. However, if these coatings are too thin, damaged, or improperly applied, the underlying metal can become exposed and susceptible to corrosion.
Operational Factors
High Current Loads: Excessive current passing through a header connector can cause localized heating, which may weaken protective coatings and accelerate the corrosion process.
Mechanical Stress: Vibration, pressure, and other mechanical stresses can lead to micro-cracks in the connector’s protective coatings, providing a pathway for moisture and corrosive substances to reach the metal surface.
Ⅱ. Common Types of Corrosion Affecting Header Connectors
There are several types of corrosion that can affect header connectors, each with its own characteristics and consequences.
Uniform Corrosion
Uniform corrosion is the most straightforward type, where the entire surface of the connector corrodes at a consistent rate. While it might seem less severe because it’s predictable and uniform, it still gradually degrades the connector’s material, leading to thinning and eventual failure.
Pitting Corrosion
Pitting is a more insidious form of corrosion, causing small, localized pits or holes on the metal surface. These pits can penetrate deep into the material, making them difficult to detect and repair. Over time, pitting can severely compromise the integrity of the header connector.
Crevice Corrosion
Crevice corrosion occurs in areas where there is a small gap or crevice, such as between two mating surfaces or under a washer. In these confined spaces, oxygen levels can drop, creating an environment that promotes corrosion. This type of corrosion is particularly dangerous because it often goes unnoticed until significant damage has occurred.
Galvanic Corrosion
As mentioned earlier, galvanic corrosion happens when two different metals are in contact in a corrosive environment. The more anodic metal will corrode faster, potentially leading to premature failure of the header connector.
Stress Corrosion Cracking
This type of corrosion occurs when a header connector is subjected to both mechanical stress and a corrosive environment. The combination can cause cracks to form, which can propagate quickly and lead to catastrophic failure.
Ⅲ. Corrosion Prevention Strategies for Header Connectors
Preventing corrosion in header connectors requires a multi-faceted approach, combining material selection, design considerations, protective coatings, and environmental controls.
Material Selection
Choosing the right materials for your header connectors is the first line of defense against corrosion.
Corrosion-Resistant Alloys: Metals like stainless steel, titanium, and certain aluminum alloys offer excellent resistance to corrosion. Using these materials can significantly extend the life of your connectors, especially in harsh environments.
Avoidance of Dissimilar Metals: To prevent galvanic corrosion, it’s important to avoid pairing dissimilar metals. If it’s necessary to use different metals, consider adding an insulating barrier between them to prevent direct contact.
Protective Coatings
Applying protective coatings to header connectors is an effective way to shield them from corrosive elements.
Electroplating: Nickel, gold, and tin electroplating are common practices that provide a thin, durable layer of protection against corrosion. Gold plating is particularly effective due to its excellent conductivity and resistance to oxidation.
Organic Coatings: Coatings made from epoxy, polyurethane, or other organic materials can create a barrier that prevents moisture and chemicals from reaching the metal surface.
Self-Healing Coatings: Some advanced coatings are designed to repair themselves when damaged, sealing any cracks or scratches that could allow corrosive elements to penetrate.
Design Considerations
Smart design choices can reduce the risk of corrosion.
Minimizing Gaps and Crevices: Design connectors with tight tolerances and minimal gaps to reduce the likelihood of crevice corrosion.
Proper Ventilation: Ensure adequate airflow around connectors to prevent moisture buildup, which can lead to corrosion.
Environmental Controls
Controlling the environment around your header connectors can also help prevent corrosion.
Humidity Control: In environments with high humidity, use dehumidifiers or desiccants to keep moisture levels low.
Regular Cleaning and Maintenance: Remove any contaminants from the surface of the connectors to prevent corrosion. This is especially important in industrial environments where chemicals or salt may be present.
Ⅳ. Corrosion Protection in Specific Environments
Different environments pose unique challenges when it comes to protecting header connectors from corrosion.
Marine Environments
Saltwater Resistance: In marine environments, using materials like stainless steel or titanium is crucial due to their resistance to saltwater corrosion. Additionally, applying specialized marine-grade coatings can provide extra protection.
Regular Maintenance Protocols: Given the harsh conditions, routine inspections and cleaning are necessary to prevent the accumulation of salt and other corrosive substances.
Industrial Environments
Chemical Resistance: In industrial settings where exposure to chemicals is common, selecting materials and coatings that are resistant to specific chemicals is key. For example, fluoropolymer coatings can provide excellent resistance to aggressive industrial chemicals.
Isolated Enclosures: Enclosing header connectors in protective housings or boxes can shield them from exposure to corrosive chemicals.
Extreme Temperature Environments
Temperature-Resistant Materials: Choose materials and coatings that maintain their integrity under extreme temperatures. For example, ceramic-based coatings can provide excellent protection at high temperatures.
Thermal Cycling Considerations: Design connectors to accommodate thermal expansion and contraction, which can otherwise lead to cracks and corrosion.
Ⅴ. Emerging Trends in Corrosion Protection Technologies
As technology advances, new methods for protecting header connectors from corrosion are emerging.
Nanotechnology in Coatings
Nanocoatings are ultra-thin layers applied at the molecular level, offering superior protection against corrosion. These coatings are highly effective in repelling water, preventing oxidation, and providing a durable barrier that traditional coatings can’t match.
Smart Coatings
Smart coatings are a cutting-edge technology that responds to environmental changes. For example, if the coating detects the beginning of a corrosion process, it can activate a protective mechanism to prevent further damage.
Advanced Material Science
Innovations in material science are leading to the development of new alloys and composites that are inherently resistant to corrosion. For instance, graphene-based materials are showing promise in providing superior protection due to their high strength and resistance to chemical reactions.
Real-Time Corrosion Monitoring
Some electronic connector companies are now integrating sensors into connectors that monitor for signs of corrosion in real-time. This technology allows for proactive maintenance, alerting operators to potential issues before they lead to failure.
Ⅵ. Conclusion
Protecting header connectors from corrosion is essential for ensuring the reliability and longevity of your electronic systems. By understanding the causes and types of corrosion that can impact connectors, and implementing effective prevention strategies, you can greatly reduce the risk of connector failure. Whether you’re dealing with marine, industrial, or extreme temperature environments, tailored solutions and emerging technologies can provide the protection your connectors need. As technology continues to evolve, the tools and materials available for combating corrosion will only get better, offering new ways to safeguard the critical connections in our electronic world.
If you’re looking for a reliable solution to protect against corrosion, we highly recommend checking out the KR2013 Series Box Header Connector from Konnra. Designed with durability and performance in mind, this connector is built to withstand harsh conditions and ensure long-lasting connections. Visit Konnra today to learn more about the KR2013 Series and other high-quality connectors and harnesses that can keep your projects running smoothly.