- The length of the trunk and branches of the automotive electrical wiring harness must be designed reasonably.
The length of the main line of the wiring harness is generally based on the actual location of the electrical appliances on the car, and then the length of each section of the wiring harness is reasonably designed. If the automobile wiring harness is designed to be too long, it will not only cause a waste of materials, but also take up too much space. The accumulated wire harness not only affects the appearance, but also easily rubs against surrounding components during vehicle driving, causing wire harness wear and electrical faults such as short circuit or open circuit. If the harness design is too short, assembly will be difficult or impossible. Therefore, the length design of the wire harness must consider the actual wiring path, and a length slightly longer than the actual length can be used to ensure the reliability of the actual wire harness assembly.

Sufficient length should be reserved for the branches of the wire harness according to the assembly of the electrical appliance. The reserved amount of the connector on the wire harness should be appropriately increased according to the installation depth of the electrical appliance, the location and opening direction of the socket, as well as the rear space and length after assembly.
Take the connector in the middle of the electrical appliance as an example: reserved length L = electrical installation depth h + electrical panel width 0.7B + 100mm. The installation depth h of an electrical device is the distance from the outer decorative surface to the internal electrical device connection socket after the electrical device is assembled. Width of electrical installation panel 0.7B: approximately 0.7 times the height of the decorative surface before electrical installation.
For other connectors of the wire harness, appropriate length should be reserved on the premise that the wire harness is easy to disassemble. It should be noted that the insertion direction of the electrical connector must leave a space greater than 2 times the length of the connector.
- The selection and arrangement of connectors should consider the convenience and rationality of assembly.
Connectors in the same area need to be distinguished by color, size and internal positioning to prevent mis-mating. Connectors should be located where they are easy to find and allow enough space for manual operation or use of tools. If the installation of the electrical device is relatively concealed and later maintenance and disassembly are difficult, the branch length of the plug-in connector should be appropriately increased to facilitate actual inspection and maintenance.
The selection of connectors must comply with standard requirements, and at the same time, the driving process of the car must be considered to adapt to long-term high-speed operation. The oil and dust accumulated in the vehicle’s mechanical system will corrode connectors and terminals for a long time, easily lead to aging of connectors and terminals, loosen the sheath of plug-in connectors, and even corrode connectors and terminals.
Relevant statistics show that electrical system problems caused by the aging of automobile wiring harness connectors and terminals account for 2/3 of the entire automobile electrical system problems. Therefore, in order to improve the reliability of wire harness design, under the same electrical parameter requirements, connectors with more reliable quality should be selected. For exposed high-current metal terminals, such as wiring terminals on switches and starters, corresponding rubber parts must be designed to protect them from accidental short circuits.
- Movement inspection of the wiring harness is required
The wiring harness of moving parts or opening and closing parts (such as doors, etc.) on the car needs to be reserved according to the maximum opening. The stacking space and fixation method of the wiring harness at the minimum opening of the component should also be considered. All wiring harnesses placed near moving parts should maintain a minimum clearance of 50 mm from the moving parts.
Analysis of key points of automotive electrical wiring harness assembly
- The wiring harness fixing points should be reasonably arranged to ensure reliable fixing.
The layout of the wire harness should consider the weight of the wire harness, the convenience of the fixing method and the fixing position, and set up sufficient and reasonable fixing points to fix the wire harness to avoid sagging and shifting of the wire harness. Figure 1 shows how to secure the ceiling harness. Depending on the direction of the wire harness and the characteristics of the car body, the distance between two adjacent fixed points generally does not exceed 300mm. At the same time, sharp inflection points should be avoided, and mounting holes should be provided at each end of the inflection point when passing through the inflection point at a vertical angle.
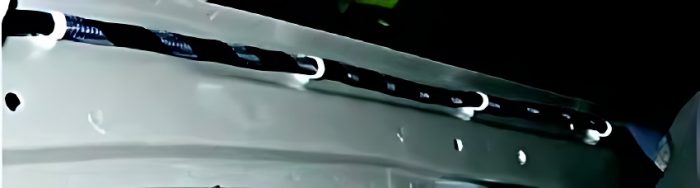
At the end of the wire harness and the insertion point of the electrical device, a fixing point should be set no more than 150mm in front of the connector. Set a fixed point at the branch point on the main line. The distance between the fixed point and the branch point should not be greater than 100mm. Figure 2 shows the fixing method of the branch wiring harness of electrical equipment.
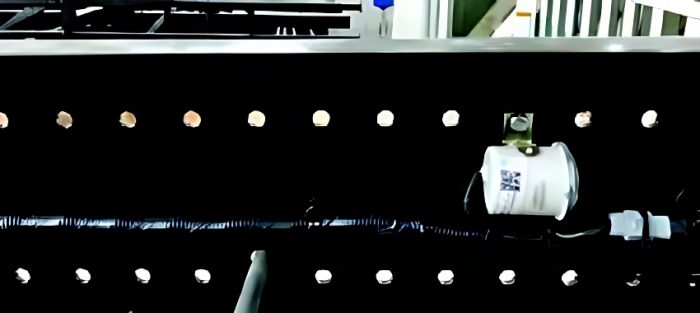
- Precautions when connecting the wiring harness to special components
Moving parts on your car include the gas pedal, brake pedal, clutch pedal, steering column, seats, and wiper motors. When arranging wire harnesses in the area of moving parts, the gap between the fixed point and the moving parts should be kept at a safe distance of more than 25mm.
When the wiring harness is close to a heat source, try to stay away from the heat source. The distance to parts with temperatures above 150 °C must be greater than 50 mm. If the wiring location cannot avoid high-temperature areas such as exhaust pipes, a heat insulation pad should be added to protect the wire harness, and the distance should be at least 125mm to effectively reduce the temperature around the wire harness.
The layout of the wiring harness should consider preventing electromagnetic interference. The signal lines of the controller and related sensor branches should be kept as far away from interference sources as possible, such as electric speakers, motors and other electrical equipment. When the sensor branch is adjacent to the power line of a high-current component, the distance should be greater than 300mm to avoid signal interference.
- Assembly process of ground wires
The grounding point is set on the body structure and chassis. The location of the grounding point requires a flat contact area so that rainwater does not collect. That is, the conductive cross section is large, the voltage drop is small, and the grounding point will not cause poor contact due to corrosion.
- Craftsmanship and aesthetics of wire harness assembly
The wiring harness should be oriented in the same direction as the accessory. The trunk wiring harness should be arranged as tilted as possible, and buckles, clips, and brackets can be used to make the overall layout of the wiring harness beautiful and neat. Corresponding rubber wire holes should be provided to allow the wire harness to pass through the sheet metal. The wiring principle of the chassis wire harness is to run the wires along the inside of the frame and try to avoid running the wires outside the frame. When passing a beam, if you can run the wire under the beam, try not to run it on the beam. The wiring layout of the wire harness branches should be smooth and reasonable, and no detours or bends should occur, as shown in Figure 3. For areas where the wiring harness distribution is relatively concentrated and there are many branches, the overall wiring harness protective cover can be considered to make the overall layout of the wiring harness beautiful and regular.
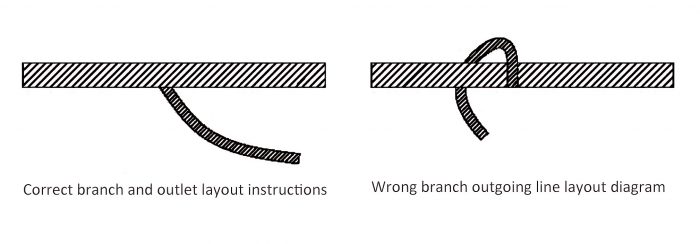
The layout of automobile wiring harness is a complex and important process. Unreasonable wiring harness layout may cause faults such as wire harness disconnection or disconnection of connector terminals, affecting electrical functions, and may lead to serious accidents such as wire harness fires. This article provides a basic description of wire harness layout. In the actual assembly layout, technicians need to continuously explore, accumulate experience, and develop more appropriate wiring paths and methods.